The Role of AI and Machine Learning in CNC Machining
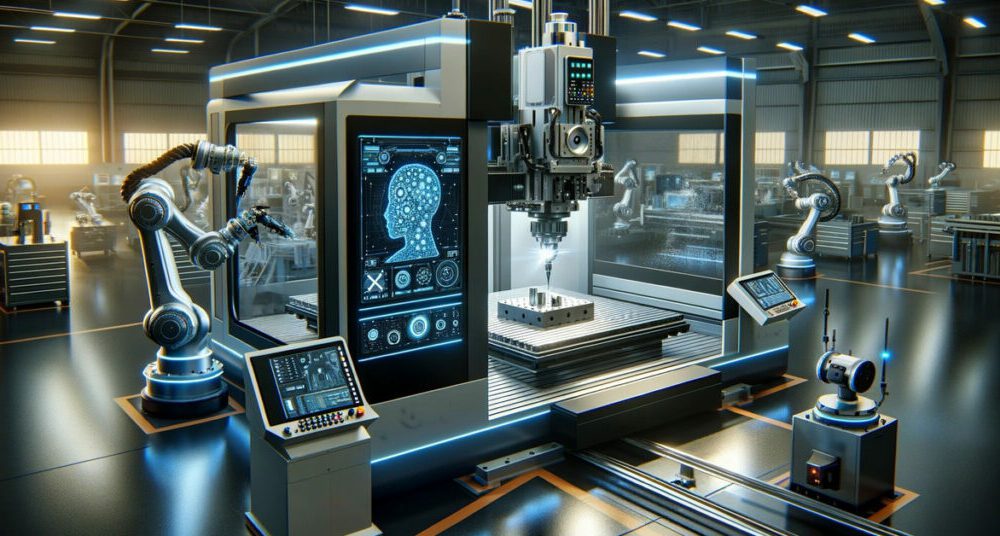
Computer Numerical Control (CNC) machining is a key component of precision engineering in the dynamic field of manufacturing. CNC machining has come a long way, from manual processes in the early days to automated CNC systems today, all thanks to unceasing innovation and technical improvement. The use of Artificial Intelligence (AI) and Machine Learning (ML) in online CNC machining service processes has been one of the biggest advancements in recent years. Keep reading this article and learn more as we examine the significant influence of AI and ML on CNC machining, covering their history, uses, advantages, drawbacks, and factors to take into account.
The Evolution of CNC Machining
In the past, a great deal of physical work was used in manufacturing operations. Machinists would carefully use tools to form raw materials into final goods. However the advent of CNC machining, which automated the control of milling machines using pre-programmed instructions, completely changed this shift. This change allowed for mass production with previously unheard-of efficiency while simultaneously improving precision and reproducibility.
The incorporation of cutting-edge technologies has improved CNC machining throughout time. The integration of AI and ML algorithms into machining systems is one such development. A new era of digital manufacturing network is being brought in by these technologies, which enable machines to evaluate massive volumes of data, adapt to dynamic conditions, and maximize performance in real time.
The Integration of AI and ML in CNC Machining
Understanding the basic ideas behind AI and ML in CNC machining is important before exploring these technologies’ applications. Artificial intellect (AI) is the replication of human intellect in machines that allows them to see, think, and act on their own. As a branch of artificial intelligence, machine learning (ML) focuses on creating algorithms that let computers learn from data and get better over time without needing to be explicitly programmed.
AI and ML algorithms are superior at processing complicated, unstructured data and extracting insights from patterns and trends, in contrast to traditional computer systems that rely on predetermined rules and instructions. These capabilities have several uses in the field of CNC machining, from predictive maintenance to process improvement.
Benefits of AI and ML in CNC Machining
The CNC machining process can benefit greatly from the integration of AI and ML, which is changing component manufacturing. Among the principal benefits are:
-
Increased precision and accuracy
AI-powered algorithms can analyze sensor data in real time to adjust machining parameters dynamically, ensuring optimal precision and accuracy throughout the production process.
-
Enhanced efficiency and productivity
Algorithms using machine learning (ML) have the potential to significantly increase productivity and efficiency by optimizing tool routes, minimizing material waste, and reducing cycle times.
-
Predictive maintenance and reduced downtime
Artificial intelligence (AI) systems can anticipate possible equipment breakdowns by evaluating equipment performance data. This enables proactive maintenance interventions and reduces unscheduled downtime.
-
Customization and adaptability to complex tasks
Artificial intelligence (AI)-powered CNC systems can adjust to changing production demands and carry out intricate operations with a high level of customization, meeting the many demands of contemporary manufacturing.
-
Better quality control
Manufacturers may identify and correct flaws or deviations from specifications right away, improving overall product quality and minimizing rework, by using AI and ML algorithms to analyze data from sensors and quality inspection systems in real-time.
Challenges and Considerations
Even though AI and ML have the potential to revolutionize CNC machining, several obstacles need to be overcome in order to fully reap their rewards:
-
Technical and operational challenges
For manufacturers, integrating AI and ML into CNC machining presents both operational and technical obstacles because it calls for a strong infrastructure, dependable data sources, and system integration.
-
Cost implications and ROI analysis
Although AI and ML technologies hold great potential for advancement, they might come with hefty upfront and continuous maintenance expenditures. For manufacturers to successfully justify these investments, a comprehensive ROI study is necessary.
-
Taking care of the workforce training and skills gap
To make the most of AI and ML, a workforce with the necessary skills to create, deploy, and support these technologies is needed. For adoption to be effective, the skills gap must be closed through efforts for upskilling and training.
Conclusion
A major change in CNC machining has been brought about by the integration of AI and ML, opening up new avenues for precision engineering and intelligent production. Manufacturers can attain previously unheard-of levels of accuracy, productivity, and customization while reducing operational risks through predictive maintenance by utilizing AI-powered algorithms. However, achieving these advantages necessitates giving significant thought to operational, workforce, and technical difficulties.
Artificial intelligence (AI) and machine learning (ML) will surely be crucial in influencing CNC machining in the future, spurring innovation, and creating competitive advantage in the worldwide market as the manufacturing sector continues to embrace digital transformation.